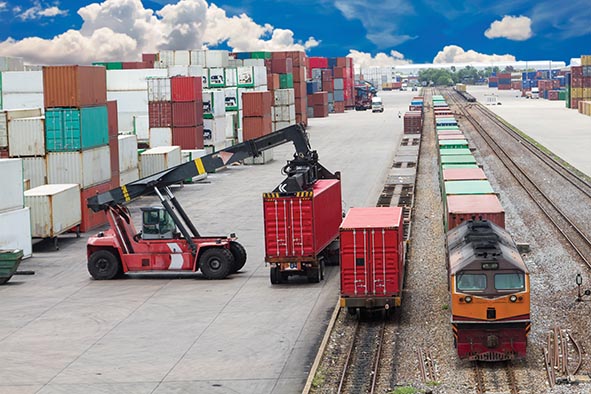
Intermodal Methodology Frees Up Faster Freight Distribution
12 Apr, 2017
Whatever method or combination of methods are used, the bottom line is getting products to market faster and more efficiently than ever.
The combination of transportation elements that make up intermodal transportation – ships, trucks, planes and trains – was created around the late 1980s when the “just in time” delivery system for manufacturers gained momentum.
To expedite delivery of products and parts needed to meet ever tighter manufacturing deadlines, containers used in cargo that was shipped on ocean carriers stayed in those containers,???? and were transported by trains and trucks faster and in a more economically feasible way.
Today, intermodal delivery happens for nearly all goods that can fit into an ocean shipping container.
Every day the nation’s commercial carriers deliver over 30 million tons of freight using one or more modes of transportation, according to a report by the Center for Intermodal Freight
Transportation done for the U.S. Department of Transportation (USDOT).
Freight movement is expected to grow from 19,326 million tons moved in 2002 to 37,178 million tons by 2035, according to the Office of Freight Management and Operations division of the USDOT.
That would mean a three-fold increase in dollar value of goods shipped, expected to be nearly $40 billion by 2035.
In 2015, intermodal was the largest single source of U.S. freight rail revenue, accounting for approximately 23 percent of revenue for major U.S. railroads.
In recent years, despite the weak economy, America’s freight railroads have been spending more than ever before — including $28 billion in 2014 and $30 billion in 2015 — on maintaining and growing their networks to help keep the economy moving, the USDOT reports.
Intermodal rail is just one aspect of the whole intermodal picture. Waterway transport and ocean port deliveries are other parts of the puzzle.
There are approximately 360 commercial sea, river and lake ports with 3,200 cargo and passenger terminals. Inland navigation is possible through an extensive network of 12,000 miles of waterways and 240 locks and dams. More than 38,000 domestic maritime vessels, including tugs, barges and oceangoing ships, use these waterways.
The Port of South Louisiana, Port of New Orleans and Port of Baton Rouge handle a high proportion of domestic cargo, while ports on the West Coast, such as the Port of Los Angeles and the Port of Long Beach, primarily receive imports from Asia.
And finally, freight delivered via air – smaller in tonnage but generally carrying products of higher value – is booming as well. Air cargo is the fastest growing freight mode in the United States, with tonnages growing at 4.3 percent per year and value growing at 5.0 percent per year, according to the DOT’s Freight Analysis Framework (FAF). FAF predicts that almost all air cargo commodities will see substantial growth over the next five to 10 years, with electronics, machinery, precision instruments and pharmaceuticals growing the fastest.
Currently more than 500 commercial airports and thousands of general aviation airports handle air cargo throughout the country.
FAF reports that the airport handling the most cargo tonnage in the U.S. is Memphis International Airport, which is the air hub of FedEx; second is Ted Stevens Anchorage International Airport; and third in total tonnage is the Louisville International Airport, which is the air hub of United Parcel Service.
Intermodal growth
The USDOT expects different freight transportation modes to grow at different rates.
Trucks have been rapidly gaining mode share since 1990 and will continue to do so out to 2040, according to the DOT.
Rail has also been steadily gaining mode share over the last two decades, although the USDOT expects these advances to slow down in the medium term and reverse in the long term, as several key bulk commodities play a smaller role in the economy.
Economic developers are keen to point out the differences between rail and trucking. For example, Tom Cross, the director of cargo and global logistics development for Port Lansing, Michigan, says that truckers have a limited amount of hours that they can drive per day, and are using methods to extend that using tandem driving teams. But there’s more. “You have to look at the volume that rail can bring,” Cross says. “If you are able to move a mile of shipping containers at one job as opposed to one semi at a time, just the sheer volume far beats the ability of the truck solution. When you look at the costs to move something from point A to point B, when you move via rail, it ends up being a cheaper and greener alternative as well,” he says. “So definitely looking at stuff via rail on the long haul approach is a far more efficient way to go.”
Port Lansing, located at the Capital Region International Airport, has an 8,500 foot runway to accommodate large aircraft, plus a U.S. customs staff. They would like to extend the runway to 10,000 feet soon, which is part of the master plan. “But right now, the three runways are more than adequate for what we need to do,” Cross says. “We would like to extend the one runway just so we can get that little bit of extra reach out of airplanes.”
He says that they have also entertained discussions about a multi modal railway facility being built at Lansing in the next year or two. “If that happens, that would give us access to about 50,000 containers a year, which would all be clearing international customs in the area.” That kind of capacity coming in would also open up airfreight markets for Lansing, he says.
Cross says that they benefit from having two General Motor assembly plants within 15 minutes of the airport. “GM wants to have a limited amount of parts on the assembly line, and they want to have all of their backup parts within a few miles of the actual plants,” Cross says. “So having that supply system being able to come through the airport, even if it’s just a portion of it, helps us demonstrate ‘Hey this [delivery method] is working and it’s an important thing to continue growing.”
Ports pack economic power
In southwest Louisiana, where the natural liquefied gas shipping business is huge, the two ports in Cameron Parish have joined together as the east and west Cameron ports, all as part of the Cameron Port Harbor district. “So that gives us six ports – the Port of Lake Charles and five other ports in the region,” George Swift, president and CEO of the Southwest Louisiana Economic Development Alliance, says.
Adding to their intermodal picture is the Chennault International Airport in Lake Charles, home to Northrop Grumman and AAR Aircraft Services. The airfield features a 200-foot-wide by 10,700-foot-long runway with 17-inch pavement capable of accommodating aircraft ranging in size from a small business jet to wide-body commercial airliners.
There are five large, certified development sites at the airport; four have rail frontage and all provide direct access to the airport’s runway facilities.
The southwest Louisiana port region has $44 billion in projects under construction now and almost another $70 billion in various stages of permitting and construction, Swift says. “There was the discovery of the Louisiana shale and rise of the fracking process. Now we can export gas and make it profitable. So that is what is happening here,” he says. “We are having an economic boom that is phenomenal.”
Ready for Panamax and more
The economic intermodal boom is in sight for the Port of Baltimore as well, one of only four ports on the east coast that is ready for the large Panamax ships that will be coming through the enlarged Panama Canal. Those 1,200-foot ships can carry over 14,000 containers.
The port has had 50 foot deep channels for 25 years, but now, as a result of a $1.3 billion private-public partnership with Ports America Chesapeake, they have 50 foot deep berths. They also purchased new super cranes for handling more and bigger cargo from these ships.
The new berth and the cranes went live in 2013. “The largest ship we have received so far has been a 9,300 TEUs (one TEU is one container) ship that came through the Suez Canal,” Richard Scher, the director of communications for the Port of Baltimore, says.
One hang up to development at the port is the Howard Street rail tunnel, which is heavily depended on to move cargo inland from truck to rail, but is too small to facilitate movement of the double stacked containers which have become a common means of moving cargo out of ports.
“The Howard Street rail tunnel is a huge project for the Port of Baltimore,” Scher says. “The Maryland Department of Transportation officially applied for fast lane funding for the tunnel. We have not heard of a decision yet. But we are cautiously optimistic that we will be successful. We have both eyes on the fast lane process.”
When the $425 million tunnel expansion project is complete, Scher says, it’s going to open up avenues to the Midwest for the port. “Right now, the vast majority of our container business is for what we call local consumption – more for consumers in this region,” he says. “We are already the furthest inland east coast port to the Midwest. So reaching the Midwestern population markets is an easy deal for Baltimore,” he says.
Once the tunnel is expanded, 178,000 containers that now leave the port on tractor-trailers each year could be moved by rail.
Efficiencies to come
According to a USDOT study, two advancements that could increase the efficiency of the U.S. intermodal transportation system are the containers-on-barge (COB) methodology, where containers are transported on the inland waterway system via towboats with specially fitted deck barges that stack containers in a similar fashion to ocean-going cargo ships. This will move more cargo off trucks in heavily congested coastal corridors to increase mobility, reliability and reduce pollution.
Whatever method is used to satisfy the country’s demand, which has increased in part because of heavier e-commerce activity requiring larger distribution centers shipping more goods, a key concern is keeping the physical infrastructure of roads, bridges and tunnels in good working order while finding new, innovative ways of getting more cargo to its destination.
Related Posts
-
Pinellas County, Florida Celebrates Ribbon Cutting of the ARK Innovation Center Business Incubator
-
Agri-technology adoption begins in earnest amidst the digitization of farming
-
New Sustainability, New Power Handling Ideas are Part of Data Center Evolution
-
Time To “Pivot, Stretch, And Adapt”
-
A Huge Industry Begins Reworking Itself
-
More Efficient Agriculture Techniques are Coming into the Focus
-
Logistics Getting on a Quicker, more Focused Track
-
Airports Signaling There’s a Recovery on the Horizon
-
Opportunity Zones and Post-COVID-19 Economic Recovery
-
New Ideas Emerge for Both Sustainable and Fossil Fuel Technologies