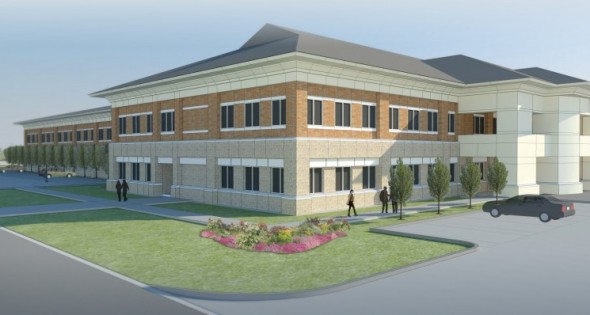
Dedicated Training Center is Louisiana’s Latest Workforce Solution
31 Jul, 2013
By Maggie Heyn Richardson
Facility answers the evolving needs of current and future advanced manufacturing companies in the region.
As the competition for major projects intensifies, some states are upping the ante on how far they are willing to go to win big investments. In Louisiana, a $22 million state and locally funded workforce training center is being built to train the workforce of German-based Benteler Steel/Tube. The company announced a $900 million investment in North Louisiana last year — marking the second largest capital investment in the U.S. during 2012.
“Benteler has a variety of jobs to fill — from administrative to engineering to technical, and the availability of a skilled, proven workforce was a major factor in choosing north Louisiana for our first U.S. manufacturing facility,” says Matthias Jaeger, president and CEO of Benteler Steel/Tube. “We are making a major long-term commitment to the Shreveport-Bossier area, so we need to have certainty about the workforce of the future.”
The steel tube manufacturer will build a two-phase, 1.35 million-square-foot facility on 330 acres at the Port of Caddo-Bossier in Shreveport. After evaluating more than 100 sites in 13 states, Benteler chose north Louisiana, in part because of its proximity to the energy sector. The company’s seamless steel tubes are among others used for exploratory drilling in the United States.
Louisiana presented an aggressive incentive package funded by nine state and local partners, but its most convincing component seemed to be the 65,000-square-foot workforce training center, underway now at Bossier Parish Community College or BPCC. Such facilities have been more common in the auto industry, but not in the industrial sector. The facility will be the first of its kind in steel manufacturing.
“The facility is an essential factor,” Jaeger says. “It helps upgrade the entire regional workforce, creating a deeper reservoir of skilled workers, and for Benteler, it ensures a supply of people are eager to be part of the next generation of innovation in steel tube manufacturing.”
Scheduled for completion in May 2015, a few months ahead of the opening of first phase of the steel mill, the training center will replicate Benteler’s manufacturing environment and will prepare Benteler’s 675-person workforce.
Louisiana Economic Development (LED) FastStart, ranked the No. 1 state workforce training program in the country, along with BPCC, will design and run the training center’s programs. LED FastStart’s Executive Director Jeff Lynn says the center will be able to simulate most of the seamless steel tube processes used by the company, including a complete ghost rolling station.
“We will house systems for Benteler that will mimic the flow of work in their new facility,” Lynn says. “We’ll be able to train their operators and technicians on their entire processes within our training center.”
BPCC Chancellor Jim Henderson and LED officials flew to Paderborn, Germany to observe Benteler’s workflow and production cycle first-hand at its main steel/tube mill.
“It was extremely valuable to see the Paderborn plant,” Henderson says. “It gave us a concrete understanding of Benteler’s process and culture, the high-tech skill set required at its north Louisiana facility and how we can craft curriculum to support the company’s ongoing workforce needs.”
The training center is designed to be highly flexible. Half of the space will initially be dedicated to Benteler. The other half will support BPCC’s expanding advanced manufacturing curriculum and will include classrooms, e-training technologies and laboratories. The goal was to establish a facility that answers the evolving needs of current and future advanced manufacturing companies in the region, says Scott Martinez, president, North Louisiana Economic Partnership.
“We have Benteler moving to northwest Louisiana, we have Ronpak opening the first paper bag plant in 10 years in the country here and we have other longtime, established manufacturers,” Martinez says. “The plan was to develop a flexible, state-of-the-art training center that can respond to the needs of advancing manufacturing.”
The Benteler team will work closely with BPCC to develop curriculum and customized programs that will train skilled steel manufacturers and operators, electrical specialists and maintenance experts.
“Our immediate priority,” Jaegar says, “is to have the training program running apace with our construction program so that we are ready to begin production just as soon as the facility is built and operational.”
Illustrations courtesy of Benteler Steel/Tube.