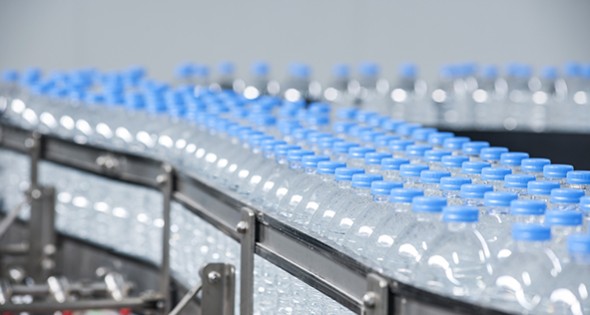
Northeastern Pennsylvania has Lowest Operating Costs for Food and Plastics Manufacturing
03 Aug, 2017
Two independently produced studies show that Northeastern Pennsylvania is one of the best locations in the country for companies looking to open new food and plastics manufacturing facilities.
The Boyd Company, an internationally recognized site location firm based in Princeton, New Jersey, recently compared cities across the country to Northeastern PA. The Boyd studies show that Northeastern PA has the lowest food and plastics manufacturing costs among those surveyed.
Both studies looked at comparative annual operating costs which included site acquisition and construction, taxes, utilities and labor. Locations studied included metro areas in New England, New York and New Jersey, Baltimore, and several areas within Pennsylvania.
“These studies reaffirm what we have been saying for years. Companies that are looking to grow their business on the East Coast should be looking at all that our region has to offer,” said John Augustine, President/CEO of Penn’s Northeast. “The majority of the US population is located within a one-day drive of Northeastern PA.”
The Comparative Annual Operation Cost Analysis studies focused on the elements that were considered the most essential to the corporate site selection process, including comparative labor costs, comparative electric power and natural gas costs, land acquisition and construction costs and property and sales tax costs.
In the report, Northeastern Pennsylvania ranked the lowest in total annual operating costs among 10 MSAs for food/beverage manufacturing and eight MSAs for plastics manufacturing. These findings are hardly surprising to those in Northeastern PA, as the region is already home to some of the top companies in the food processing and plastics clusters.
To create the comparison, the food/beverage study used a hypothetical 225,000-square-foot production facility employing 350 workers. Operating cost differentials were based on the latest first-quarter 2017 figures. The report was designed to compare costs across various food and beverage processing industry sectors.
For the plastics study, the overall operating costs were compiled for each region using a hypothetical 175,000-square-foot facility with 225 employees. The operating cost differentials were based on the latest third-quarter 2016 figures.
Related Posts
-
IONNA, LLC, to Invest $10M in Global Headquarters in Durham, North Carolina, Creating 203 Jobs
-
Construction, Manufacturing and Fabrication Innovator RNGD Invests $25 Million to Expand Southeast Louisiana Operations, Create 130 Direct New Jobs
-
Novo Nordisk to Expand Johnston County, NC Operations with $4.1B Investment, Creating 1,000 New Jobs
-
Gov Kemp: Food Solutions Company Cargill to Create 400 New Jobs in Metro Atlanta Office Hub
-
RoyOMartin Announces $30 Million Modernization of Timber Manufacturing Facility in Southwest Louisiana
-
Four Business Expansions Bring 144 Jobs to Kent, Bay Counties
-
Sodexo Opens Its New North American Headquarters
-
FUJIFILM Diosynth Invests $1.2B in Holly Springs, North Carolina, Manufacturing Facility, Creating 680 New Jobs
-
Eastman’s second U.S. molecular recycling facility will be in Longview, Texas
-
Wisk and the City of Sugar Land, Texas, Partner to Bring Autonomous Air Taxis to the Greater Houston Region