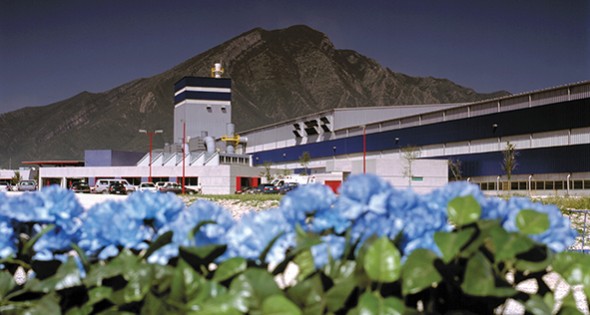
Advanced Manufacturing Ecosystem Widens & Connects
11 Aug, 2017
Innovations begin to make their impact as more applications filter into other industries.
The American economy hinges on better use of innovative technology to not only save production costs but advance new ideas in products and services that the rest of the world depends on.
Advanced manufacturing includes aerospace products and parts; automobiles products and parts; electric power generation, transmission and distribution; construction and mining machinery; navigation, measurement and control instruments; metal ore mining, aluminum production and processing; chemical products; oil and gas extraction; audio and video equipment; general purpose machinery; computers, processing and hosting and peripheral equipment; medical diagnostics equipment and other scientific instruments; and more.
A report from Economic Modeling Specialists, Inc., (EMSI) helps organizations understand the connections between economies, people and work. It says there have been over 300,000 new jobs created in advanced manufacturing since 2011 (six percent growth), which accounts for nearly half of all new manufacturing jobs (618,000 new jobs since 2011, growing at roughly five percent).
Where there is growth
The EMSI report found that manufacturing industries made up 35 of the 50 advanced industries, including motor vehicle manufacturing, aerospace manufacturing, ship and boat building, basic chemical manufacturing, and more; 23 of the 35 advanced manufacturing industries have experienced national job growth since 2011.
There is an encouraging amount of job growth in advanced manufacturing industries, especially in southern states such as Alabama, Tennessee and Kentucky. This growth is especially impressive because advanced manufacturing typically requires fewer workers, so even when these industries are producing and earning more than they have in the recent past, they do not necessarily add jobs.
Louisville, Kentucky, has witnessed a huge surge of advanced manufacturing companies locating there (42 percent since 2011), attributed to its booming motor vehicle manufacturing industry (more than 5,000 new jobs between 2011 and 2015) as well as its motor vehicle parts manufacturing and household appliance manufacturing industries (each with over 2,500 new jobs).
According to a report by the Brookings Institute, “America’s Advanced Industries: What They Are, Where They Are and Why They Matter,” as of 2013, the 50 advanced industries employed 12.3 million workers, or about 9 percent of total U.S. employment. Even with this modest employment base, U.S. advanced industries produced $2.7 trillion in value added annually – 17 percent of all U.S. gross domestic product.
That is more than any other sector, including healthcare, finance or real estate. The sector employs 80 percent of the nation’s engineers; performs 90 percent of private-sector research and develop; generates approximately 85 percent of all U.S. patents; and accounts for 60 percent of U.S. exports.
Michigan still a hotspot
One of the priorities in Michigan is their work advancing mobility and autonomous vehicles as it relates to advanced manufacturing, according to Josh Hundt, vice president of business development projects for the Michigan Economic Development Corporation (MEDC). “Ford and GM are already at the forefront in a leadership position in this space,” Hundt says. “So we can see an opportunity to be the leader in this space of the industry.”
He pointed to research that ranks Ford and GM as number one and two respectively in the mobility space.
He also talked about the impact of the American Center for Mobility in Ypsilanti, a research and testing laboratory which is a joint initiative between the state, the MEDC and the University of Michigan. The 500-acre facility will focus on testing, verification and certification of connected and automated vehicles. “That is the first center in the nation to be doing this type of testing,” Hundt says. “So that represents a huge opportunity for us.”
The state recognizes that autonomous cars and mobility development is constantly evolving, and Michigan wants to build off their expertise from decades of manufacturing, Hundt says. “We are looking at a long-term horizon in terms of changing the industry,” he says. “But we are already seeing some of the initial versions of this autonomous space, with such things as parking assist. It’s not about predicting the future in terms of exactly where it’s going to go. It’s more about being prepared both in terms of a technological and manufacturing side for the future of this space.”
Meanwhile, it’s advanced manufacturing business as usual in the state. In 2011, a $35 billion contract was awarded to Boeing to build nearly 200 giant airborne refueling tankers for the U.S. Air Force.
Chicago-based Boeing said Michigan will benefit from about 450 jobs and an estimated $25 million in annual economic impact from the Boeing NewGen Tanker, called the KC-X. It replaces 179 of the current KC-135 aircraft.
Other Michigan companies expected to benefit from Boeing’s contract are Honeywell Aerospace in Boyne City, a division of New Jersey-based Honeywell International; Cleveland-based Eaton Corp.’s aerospace division plant in Jackson; and the Grand Rapids plant of Evendale, Ohio-based GE Aviation Systems.
Hundt says that he thinks advanced manufacturing is going to remain a key factor in economic development in Michigan, while they emphasize workforce development as the next steps.
Flying high in the south
Aerospace is high on the priority list for South Carolina as well, according to Marc Fetten, CEO of Cooper River Partners in Goose Creek working with the Charleston Regional Development Alliance. “Automotive is another one,” he says, adding that Daimler just announced a half billion investment to actually make the entire Sprinter van there, and not just assemble them as they have in the past. “That investment is underway as we speak,” Fetten says.
Volvo is also making a half billion investment, bringing in close to 2,000 employees. That project is under construction now, with the first vehicle expected to roll off of the assembly line in early 2018. “Automotive like this is uncharted territory for South Carolina as a state,” Fetten says.
The “ground for this was really plowed” by the $2.2 billion, 1,150-acre BMW manufacturing plant in Greer that opened in 1992, reportedly the company’s only assembly plant in the U.S., which has become the state’s largest exporter, Fetten says. “I think that they have exceeded $8 billion in investments in their tenure there,” he says. “They started off as a sort of small production facility. But their growth has been a function of training, a function of being in a good business environment and a function of the logistics cluster that has developed here.”
Logistics in the state includes Port Charleston, a critical asset for the auto industry, where each day, an average of six vessels sail into the port carrying cargo worth more than $150 million. “Port Charleston is the closest port to Europe,” Fetten says. “And that is a big selling point.”
He says that, in addition to automotive manufacturing, they are ramping up aerospace manufacturing. “We want to have enough critical mass that even has aerospace interior manufacturing and engine component companies looking to come here.”
Working with and helping develop companies that use composite products, like the composites used in the wing structure of Boeings’s 787, is another target for the state’s economic developers. “That whole technology expanded significantly when Toray Industries announced a big investment in upstate South Carolina,” Fetten says. Toray, a plastic resins and composites product manufacturer headquartered in Tokyo, settled in Spartanburg County in 2014 and expects to invest $1 billion in their manufacturing operations there. “So those are clusters that really start to fill out with a backbone that is solid. We are looking to building up these industries, and then work on the overlap between the different industries.”
As an example of that buildup, he cites Trident Technical College that just built a $79 million aeronautical training center at its North Charleston campus. The 215,000-square-foot space would help train workers for the aeronautical cluster in the region and state, including Boeing South Carolina and its suppliers and vendors. “But the fact of the matter is it might as well be called an advanced manufacturing training center because the skill sets that are learned there are applicable to automotive and some of the other industries that we look at here,” Fetten says. “We call that our ecosystem. It spans clusters and across clusters. So you got the industry cluster such as airplane manufacturing and it gets expanded into an ecosystem and some bio firms come here. And then to make it really work, you need what we call foundational assets like infrastructure, a port, a good road system and an educational system to support all of that for the long run.”
Sidebar
Building better buildings
Varco Pruden Buildings, a division of BlueScope Building North America, has seven manufacturing facilities across the country – among them Alabama, Missouri, North Carolina and Tennessee (Varco is headquartered in Memphis). “That gives us an advantage over other building manufacturers as far as being able to provide steel buildings and materials within various radius of miles,” Doug Yancey, advertising manager for Varco Pruden, says. “That’s important, because the cost of shipping these large and heavy steel building elements can eat you up.”
The company does 3,000 to 4,000 buildings a year of all different sizes, from 1,200 square feet to 150,000 square feet and beyond. Many of those are for big manufacturing facilities, like an automotive plant in Georgia or Mississippi. “The end-use category as far as the type of building ranges from churches and schools and office buildings to retail buildings and auto dealers,” Yancey says.
He adds that they also do a fair share of agricultural buildings, like a juice manufacturer or other food processing facilities. “We have even done some bourbon distilleries and wineries and craft breweries.”
He says that some of their manufacturing buildings have to be able to support large cranes that can lift up to 40 tons of material. “There is a marble plant that quarries stuff out of the ground and then they have to slice and dice it for kitchen counters,” Yancey says. “They have to have these heavy cranes to lift up those stones and take them from one place to another inside the building.”
Related Posts
-
Pinellas County, Florida Celebrates Ribbon Cutting of the ARK Innovation Center Business Incubator
-
Time To “Pivot, Stretch, And Adapt”
-
More Efficient Agriculture Techniques are Coming into the Focus
-
Logistics Getting on a Quicker, more Focused Track
-
Opportunity Zones and Post-COVID-19 Economic Recovery
-
New Ideas Emerge for Both Sustainable and Fossil Fuel Technologies
-
New Goals and New Internet Tech Help Build Base for Advanced Manufacturing
-
Business Services Today Focus on Human Resources, Data Analytics
-
Ready to Shift into High Gear
-
The New Forestry Momentum