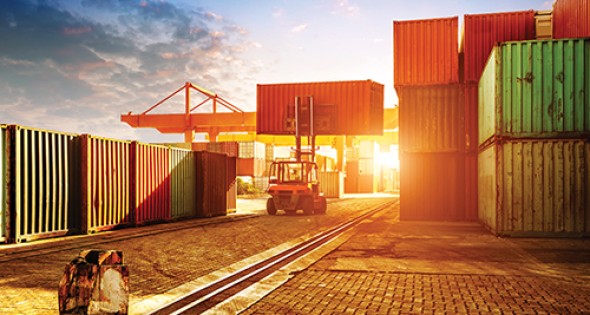
InterModal: Faster and more efficient from start to finish
27 May, 2016
E-commerce is booming, and so are the intermodal businesses that serve it
By David Hodes
The growing trend of more storage and delivery of products that has been created because of the constantly accelerating e-commerce business activity has presented both challenges and opportunities to companies in the logistics chain of transportation, distribution and delivery.
According to the U.S. Census, U.S. manufacturers reported e-commerce shipments were $3.3 trillion in 2013, up 11.1 percent from a revised $3.0 trillion in 2012.
Intermodal shipping, or the shipping of cargo using multiple modes of transportation, has enabled companies to save both time and money. Today, international cargo can reach virtually 100 percent of U.S. consumers in two to five days via intermodal, according to the Association of American Railroads.
Things are shifting, changing and adjusting in this dynamic environment, with the ever-present goal of just keeping things rolling.
“There has been a huge intermodal shift from air freight to sea containers and railroad,” says Tom Cross, director of cargo and logistics development for Michigan’s Port Lansing. “That’s because the volume that ships can actually take, up to 25,000 of these sea containers, is cheap and effective and has regular schedules that can be relied on,” he says. “Shippers are seeing that as the best way to do things because it keeps their supply chains rolling,” he says.
Down south in Mobile, Alabama, APM Terminals Mobile accelerated intermodal container shipping in the area with its port beginning in September 2008. This move was a direct result of the needs of the Hyundai plant in Montgomery, Alabama, and has also served to help attract the first U.S. factory for Airbus to the area last year.
Additionally, The Alabama State Port Authority is constructing a Phase 1, 70-acre Intermodal Container Transfer Facility (ICTF) adjacent to the container terminal at the Port of Mobile. The ICTF will be developed in multiple phases to bring rail facilities on line in time to meet import/export demand. APMT has invested $8 million in the ICTF which is scheduled to open May 1, 2016. According to Mac Taul, president of Merchants Transfer Company, an Alabama-based logistics company “Over the next five years, there is just going to be more and more here, in part because of the expansion of the Panama Canal allowing in bigger ships.”
Coming in from the Pacific Coast of Mexico are perishables that make the U.S. crossing in south Texas at the international bridge in Pharr, Texas. The $18 million, 3.2-mile-long Pharr-Reynosa International Bridge serves as one of the most important ports of entry on the U.S.-Mexico border. It connects U.S. 281 to the city of Reynosa, Tamaulipas, in Mexico.
Luis Bazan, president and CEO of Pharr Chamber of Commerce, says that the bridge is handling 2,200 trucks daily coming into the United States. Perishables account for about 60 percent of their trucking volume, but Bazan says they expect that number to double
That volume of shipped perishables is growing because of Mexico’s new, $2 billion super highway between the Pacific coast of Mexico and Texas, connecting directly to the tip of south Texas, which will soon connect directly to the international bridge. “A lot of these companies were taking product from the Pacific coast into the Nogales, Arizona, port, but they are now able to save about 800 miles, $3,000 and about 60 hours on that trip coming through here,” Bazan says.
Bigger now means taller
Not only has the amount of goods and products being shipped changed over the last few years, but the way in which it is stored is undergoing an adjustment unheard of just a few years ago.
Big box distribution centers 500,000 square feet and more are using more vertical space now as compared to a few years ago. “We are seeing buildings that are massive as far as volume goes,” Cross says. “And they are absolutely getting taller, which makes sense because people pay based on square footage, not cubic footage,” he says.
Pat Feeney, senior vice president for CBRE in Phoenix, which focuses on industrial properties, says that they just finished a 400,000-square-foot distribution facility in nearby Goodyear for REI, the outdoor recreation gear company. The building was designed with a 40-foot clear height.
“The coverage ratio between land and building is going down,” he says, referring to the percentage of land versus the percentage of building in a distribution facility’s footprint. “There are more employees now, which means you need a larger parking lot, and more trucks, which means more maneuverability space and cuing lanes, and a larger building,” he says. “Then you have larger electrical services which [are] normally a minimum of 3,000 amps and sometimes up to 9,000 amps because they want to light the building to very high standards. That and the air condition and material handling equipment take a lot of power,” he says. “So users are asking a lot of questions that they did not typically ask two or three years ago when it was just 2,000 square feet of office space in a big box facility, six people in the warehouse, two people in the office and 10 cars in the parking lot.”
Trucks vs. rail
Intermodal operators are always looking at what works best to keep the product flowing from point to point. One of the most important strategic decisions is whether to use a truck, which is better for short runs, or the railroad, which is better for large quantity shipments. “Truckers have a limited number of hours that they can drive per day,” Cross says. “You have to look at the volume that rail brings in. If you are able to move a mile of shipping containers at once as opposed to one semi at a time, just the sheer volume far beats the truck solution,” he says.
Taul says that there is a point where trucking is cheaper based on its travel miles radius, but that radius moves based on fuel costs. “So right now, a truck radius would be longer because fuel is so low,” he says. “As fuel gets lower, the radius may go from 250 miles to 300 miles.”
He says that his company ships with a mix of both truck and rail. “You will get a lot of trucks in the pipeline to make your customers happy, because they need products now,” he says. “Then you follow that up with rail shipments. With a mix of both, you can set aside your time restraints as well as saving money on the shipping side.”
Timing is everything
Cross says that they check product movement algorithms to see what is moving in and out of the state. “We know that in a couple of months it will be cherry season, and right now I am trying to work with the cherry growers to ship that stuff out of Michigan rather than do it somewhere else, like Chicago or another airport or facility,” he says. “Then blueberry season comes up later in the year, and we are going to do the same thing.”
The Port of Montana, in northwest Montana at the juncture of Interstates 15 and 90 and served by the Burlington Northern Sante Fe and Union Pacific Railroads, distributes throughout the Northwest.
Some of the products currently distributed at the port are automobiles, fuel, road deicer, steel, pipe, fertilizer, building materials and industrial sands.
Spring and fall are its highest seasons for shipments. “Right now we will start to see steel and pipe shipping picking up for some of the construction projects, like bridges or roads,” says Kathy Fasso, general manager of the Port of Montana. “We also have an automobile facility for General Motors, and there is a big influx usually for the next quarter on having vehicles for distribution coming to the state.”
She says that they are definitely looking at adding some rail track to the facility because they are starting to see some movement in liquid bulk now. “When you are shipping, you are always just reanalyzing the logistics chain,” she says. “And we want to get in front of people who are shipping bulk products into our state, and other potential customers in places like Canada who want a drop closer to their border that they can then finish picking up.”
The future
As demand for more products to be delivered faster to customers continues to grip the intermodal builders and shippers, new ideas about shipping have sprung up.
One user in Phoenix, for example, is looking to build either a 400,000-square-foot building in the outskirts of the city or three 150,000-square-foot buildings strategically located in the metro area. “That was strictly driven by quick delivery times,” Feeney says.
One of the problems in Arizona is the heat, with air-conditioning units mounted on the ceiling cooling all of the huge square footage inside. “On the floor it might be 72 degrees, but up at the roof it might be 88 or 90 degrees,” Feeney says.
REI stores Clif Bars in the building, which is a nutritional supplement bar used by hikers, and REI had a concern that those bars would get soft if stored at the top of the inside storage space near the ceiling where it would be subjected to heat. “So they installed an air-conditioning system that was guaranteed to have a variance of just two degrees from the floor to the 40-foot level,” he says. “So if you are talking about building evolution ideas, that building is one that is on steroids.”
The intermodal business is ripe for both new opportunities and new players. Cross says that he wouldn’t be surprised to see Amazon get more into the intermodal game, since the company recently signed a deal for the lease of 20 cargo planes as its first step into the air freight business. “I look at the ideas that they have and the capital that they have to back it up,” he says. “I wouldn’t be surprised to see Amazon becoming the next UPS, where they start managing other people’s supply chain and getting into their own package delivery.”
Automated driving systems have been developed for the trucking industry and are being tested now. Trucks now have computers that can predict maintenance issues, alert drivers and even get then to the nearest shop to fix a problem. GPS-guided cranes enable swifter cargo transfers in intermodal terminals, and automated optical scanners quickly and reliably identify trailers, containers and trucks as they enter and exit a transfer facility.
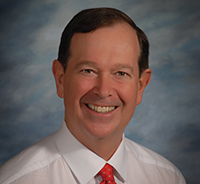
David Hodes is a freelance writer based in Arlington, Virginia, He can be reached by emailing dhodes11@gmail.com
All of this innovating and strategizing is designed to get more product moving faster and cheaper to its destination.
The e-commerce surge, far from being just another business bubble, is here to stay. “I heard that FedEx is saying that they will be raising their rates because they have had to install so much infrastructure to handle this unbelievable onslaught,” Feeney says. “It’s just an enormous increase in business.”
For more information about intermodal companies mentioned in this article, contact:
– cbre.com
Side Note
Access to success
Access to the west side of O’Hare Airport in Chicago was part of an O’Hare modernization program begun 15 years ago. The plan envisioned the reconfiguration of O’Hare’s airfield and the development of terminal and roadway access facilities on the west side of the airport.
This reconfiguration is expected to allow for expansion of terminal facilities to the west and ultimate development of western access to the airport.
It will also allow the airport to accommodate new larger aircraft, such as the Airbus.
Western access opens up that side of the airport to a whole new audience, according to John Carpenter, president and CEO of Choose DuPage, the county where O’Hare is located. Carpenter says that there are a couple different components to it: the western access and the whole O’Hare Expressway component. “The western access is contingent on the completion of the Elgin O’Hare Expressway (Illinois Route 390), and that is moving along pretty quickly,” he says.
Currently, no matter where you are coming from in the region, a commuter has to go all the way around to the east side front door of the airport to get in, he says. After the completion of the west side access, with northern and southern links to the airport as well as access to the airport, there will be many opportunities for development, he says, as well as time and dollar savings for the air traveling commuters.
“That added convenience can make it far more attractive for freight forwarders and for manufacturers who may be shipping time-sensitive materials into this area,” he says. “You don’t need to go all the way around the airport to come into the east side, or get stuck in traffic on 294 coming in from the south,” Carpenter says.
This access also opens up opportunities for mixed-use development in the county, much like the development in Rosemont expected from the $18 million extension of Balmoral Avenue that provides more direct access to the airport on the east side. One example is The Pearl, announced last August and expected to open in the fall. It is Rosemont’s newest mixed-use development. It will be an upscale mixed-use project featuring up to four unique restaurants, 100,000 square feet of office space and a 150-room boutique hotel.
DuPage has 600 acres open for development on the west side.
All of this development requires the completion of the modernization program, Carpenter says. “There is a runway that needs to be decommissioned that will free up more real estate on the west side, and that is part of the plan,” he says. “That is probably two years down the road.”
These things don’t happen quickly, he says. “These are very major projects that have to be completed in a methodical way. But all of this is part of a master plan that benefits DuPage County.”
Related Posts
-
Pinellas County, Florida Celebrates Ribbon Cutting of the ARK Innovation Center Business Incubator
-
Time To “Pivot, Stretch, And Adapt”
-
More Efficient Agriculture Techniques are Coming into the Focus
-
Logistics Getting on a Quicker, more Focused Track
-
Opportunity Zones and Post-COVID-19 Economic Recovery
-
New Ideas Emerge for Both Sustainable and Fossil Fuel Technologies
-
New Goals and New Internet Tech Help Build Base for Advanced Manufacturing
-
Business Services Today Focus on Human Resources, Data Analytics
-
Ready to Shift into High Gear
-
The New Forestry Momentum