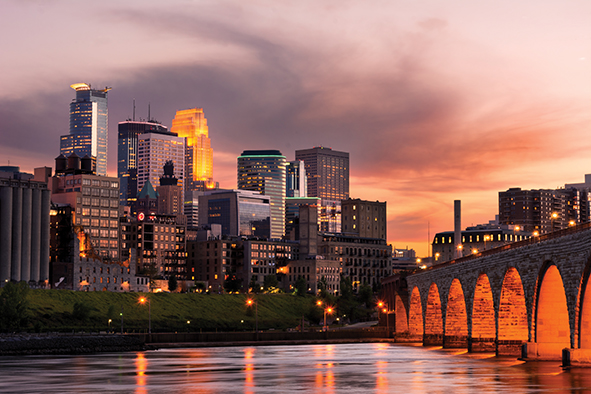
Minnesota: Homegrown Economy Built on Innovation
15 Jan, 2018
Minnesota’s strong economic performance in recent years is the result of diverse industries, a hardworking and highly educated workforce and innovation-minded businesses. Government and business working together helps make the environment conducive to job growth in a changing economy.
Grow Minnesota!, the Minnesota Chamber of Commerce’s distinctive, private-sector economic development program, has tracked four economic indicators for the past 15 years: innovation, exports, investment and workforce. Of the four, innovation is the strongest today; however, the other three are close behind. All are driving change which is key to Minnesota’s growth.
The Chamber’s mission is to make strategic changes in state policy that will help the state’s overall economy change and grow. This year, Minnesota had the most successful legislative session in several years in terms of strengthening the state’s business climate. Accomplishments include creating meaningful business tax relief; the creation of health care options with more contained costs; transportation investments without raising taxes; education investments and reforms; environmental permitting efficiencies; and investments in broadband, workforce housing and childcare facilities.
Currently, the educated and skilled workforce of Minnesota is a strength, but making sure the state has a workforce that is appropriately trained and sufficient in numbers to supply the state’s economic needs is a top priority.
Minnesota has a history and tradition in entrepreneurship of starting Fortune 500 companies. Of the state’s 17 Fortune 500 companies, 16 are homegrown in the state.
The economy is not dominated by any single industry, but is diverse with several key sectors such as biosciences, medical devices, precision manufacturing, data centers, clean technology and energy conservation, banking and finance, healthcare services, and agriculture and food.
The world renowned Mayo Clinic and the University of Minnesota form the state’s strong backbone in biosciences. The Mayo Clinic is developing a $6 billion Destination Medical Center in Rochester.
The University of Minnesota has developed the Biomedical Discovery District, which is a complex made up of the most advanced facilities for basic and translational research. It also operates the University’s Biotechnology Resource Center and its Office for Technology Commercialization, spinning off almost 20 new Minnesota business in last 12 months.
Both institutions are connected with The Hormel Institute, a state-of-the-art biomedical research center in Austin that is also expanding its laboratories and staff. Here, more than 100 scientists and collaborators conduct research to improve health.
The Minnesota Chamber of Commerce is focused on Minnesota’s future, and Grow Minnesota! helps companies realize their plans as they navigate the changing and growing economy.
Regional Sidebars
By Rachel Hamilton
City of Fairmont
Zierke Built Manufacturing (ZBM), which manufactures fuel tanks and commercial trailers moved into a 90,000-square-foot facility in Fairmont in August of 2017, says Economic Development Coordinator, Linsey Preuss.
“That’s really exciting for our community,” Preuss says, explaining that ZBM needed employees trained for welding and fabrication. “That does fit nicely with a lot of the manufacturers that we already have.”
Because the community has so many businesses in that cluster, the public school system expanded its vocational training program to include a Welding Academy in 2016, which offers classes for high school students and for adults, says Preuss.
Fairmont Foods, Inc. is expanding their food-processing facility, Preuss says. “They have a fry line and an oven line,” she explains. “This expansion allows them to run both of those lines at the same time and to double their production capacity in that area.”
Fairmont is in south central Minnesota on Interstate 90, which provides access to Interstate 35 and Des Moines, Sioux Falls and Chicago. The City owns an option on a 40-acre site off Interstate 90 and is working on the preliminary engineering for the infrastructure, says Preuss.
Fairmont has a 75,000-square-foot virtual spec building — expandable to 100,000 square feet — which has “been through plan inspection and is ready for construction,” Preuss says, explaining that the building can be customized to suit operational needs.
The area’s established industrial park has 18 certified shovel-ready acres for a company that will build a 50,000 square-foot facility and create jobs, says Preuss. “The City owns the site, so we have control over the price of the property and can offer incentives.”
The industry targets for that site are agribusiness, manufacturing or distribution. “Agribusiness is one of our targets because we are the state’s largest producer of hogs and corn and in the top ten for soybeans and cattle,” Preuss says.
“Obviously, we offer incentives for business attraction,” says Preuss, “but once someone moves in, incentives are still available.” They include Minnesota Investment Fund (MIF), tax abatement and tax increment financing (TIF).
Last year we launched a program called Fairmont Area Life [FAL],” says Preuss. The program’s goal is to attract talented workforce and to partner with the recruitment efforts of area businesses. FAL provides information about the community to prospective employees.
Wright County
“What makes Wright County so unique is we are close to the Twin Cities while retaining our rural agricultural flavor,” says Executive Director, Duane Northagen of the Wright County Economic Development Partnership. Interstate 94 runs inside the northern border of the county, connecting the Minneapolis-St. Paul (MSP) metro with St. Cloud and Fargo.
“In the last 20 years we’ve been the second-fastest growing county in the state; over the next 20, we’ll be the fastest,” says Northagen. Wright County’s population is over 132,000 now, and “will be pushing 200,000 in the next 20 years.”
Interstate access to the MSP International Airport and two rail lines help attract companies. The Otsego area has one million square feet of distribution space, including Room & Board’s 450,000 square-foot facility.
“We’ve got some 350 manufacturing-type businesses in Wright County, so we have a diverse base,” says Northagen, citing precision medical device manufacturing, fabricated metal products, prefabricated wooden products and agricultural-based ventures as the largest clusters. “Any time there’s a manufacturer, there’s a need for a secondary suppliers.”
No Name Meats, which is part of the J&B Group, has added 100,000 square feet to their manufacturing operations in 2017. “They will be Wright County’s first $1 billion per year business,” says Northagen.
Industrial Louvers Inc. (ILI) designs and manufactures architectural louvers, equipment screens, decorative grilles, sunshades and column covers. ILI broke ground in August 2017 on a 30,000-square-foot expansion in Delano, Northagen says.
Sil-Pro, also located in Delano, is a contract manufacturer for the healthcare, aerospace and defense industries. They will break ground in 2018 on a 50,000-square-foot operations and manufacturing facility. “For the past year and a half, they have been doing internal expansion and adding about 100 employees per year,” says Northagen.
“Another key company is Ultra Machining Corp. [UMC] in Monticello,” Northagen says, noting that UMC has over 200 employees in its 72,000-square-foot facility. UMC provides precision manufacturing for the medical device and aerospace industries and was named Best in Class in the 2015 Minnesota Manufacturing Awards.
Carpentry Contractors Company (CCC) in Montrose builds wall and floor panels in a controlled manufacturing environment and transports them to residential or professional construction site where their carpenters put the homes together.
City of Albert Lea
Albert Lea is at the intersection of Interstates 35 and 90 in Southeast Minnesota, roughly halfway between Des Moines and Minneapolis. The city has “a strong history of manufacturing [going] back to just after World War II,” says Executive Director Ryan Nolander of the Albert Lea Economic Development Agency (ALEDA).
“We’re well diversified,” says Nolander. “Our strong history has been in food processing, and we continue to have a huge presence in that sector.” Examples include Mrs. Gerry’s Kitchen, Ventura Foods and Albert Lea Select Foods.
Metal fabrication is also important in Albert Lea, Nolander says. “We’re really good at advanced manufacturing and food processing.” Because of the city’s intersecting interstates, they also attract distribution centers.
ALEDA “has over 200 acres of land under our control for development,” says Nolander. That includes the ALEDA Industrial Park’s 70 available acres. ALEDA owns five industrial buildings for lease; one of those, a 62,500-square-foot facility, will become available in January 2018.
ALEDA tailors incentives “project-by-project,” Nolander says. “Some businesses need to offset upfront building costs; some prefer tax abatements over time to offset long-term operational costs. We like to get with the companies and look at what’s best for them and design something accordingly.”
“Recently we partnered with a food processor in town to construct a new building which we will lease to them so they can put their capital toward job creation and new equipment,” Nolander says. Zumbro River Brand has roughly 115 employees now, and this project will allow them to create 20 new jobs.
“Workforce is the major hurdle to economic development right now,” Nolander says, explaining that in Albert Lea, as in many non-urban areas of the U.S., younger generations in the workforce are not able to replace the sheer numbers of retiring baby boomers.
“As a region, Southeast Minnesota is trying to be proactive to recruit people to our part of the country,” Nolander says. ALEDA is working with higher education institutions in the region to help students gain internships and form professional connections in the area. Those connections added to family ties, he says, can be a persuasive argument for people to return to Albert Lea.
City of Brooklyn Park
Brooklyn Park is north of Minneapolis along Interstate 94 and State Highway 610. “Businesses are growing or moving here because we have land, and you can build a manufacturing facility,” says Economic Development and Housing Director Erik Hansen of the Brooklyn Park Economic Development Division.
“Twenty percent of our industry base is in high-volume manufacturing,” Hansen says, noting that manufacturers are doing a lot of their expanding along the 610 Corridor. Access to trucking routes and proximity to local colleges and technical schools give the city an advantage in precision manufacturing.
International companies seeking to establish facilities in the U.S. are attracted to Brooklyn Park. Olympus Surgical Technology from Japan, Nilfisk, a cleaning equipment manufacturer from Denmark, and Wurth-Adams, a manufacturer of fasteners from Germany, have all located their headquarters, R&D and manufacturing facilities in Brooklyn Park, says Hansen.
“We also have home-grown industries in plastics,” Hansen says. Diversified Plastics Inc. (DPI) recently celebrated 40 years in Brooklyn Park and has created three components for the Juno Probe that is currently orbiting Jupiter.
The City of Brooklyn Park is starting a new marketing campaign to highlight the products created in the city. The Built in Brooklyn Park initiative is aimed at “demystifying the manufacturing industry” for prospective employees in particular and showing “what modern manufacturing looks like — it’s brightly lit and high-tech,” Hansen says. DPI is one example.
Brooklyn Park is partnering with neighboring city Brooklyn Center on a workforce program called BrookLynk, “a youth career exploration and internship program for kids with barriers,” says Hansen, explaining that “like many cities, there’s a [socioeconomic] disparity between white people and people of color; we’re trying to address our areas of poverty.”
North Hennepin Community College and Hennepin Technical College “customize training for employers and create pathways in Brooklyn Park for people who are looking for work,” says Hansen. “We’re trying not only to attract people to move to Brooklyn Park, but also to take people who are unemployed or under-employed and give them as many opportunities as we can.”
The Minneapolis-St. Paul metro has two light rail transit lines; both are planning to expand their reach to the suburban metro. The future Metro Blue Line Extension has five stops planned for Brooklyn Park. Those stops will be adjacent to business opportunities and educational institutions, according to Hansen.
Brooklyn Park’s Business Forward initiative advises the City on regulations and processes that could be made more business-friendly, Hansen says. It is now joined by the Brooklyn Park Development Corporation (BPDC), which can provide loans for small businesses.
Business Forward hosts yearly events open to the over 1,300 businesses in Brooklyn Park, and has become a place for local business leaders to share their successes, to network and to connect with each other and the city, says Hansen.
Related Posts
-
Business Starts Here
-
TEXAS ENTERS 2021 AS WORLD’S 9TH LARGEST ECONOMY BY GDP
-
CALIFORNIA: 5TH LARGEST ECONOMY IN THE WORLD
-
MINNESOTA: FIRST IN FIVE-YEAR BUSINESS SURVIVAL RATE
-
CANADA: Alberta. More Open Than Ever
-
KENTUCKY: The Bluegrass State Is The Right Place To Grow Your Business
-
TENNESSEE: Great Brands Deserve the Great State of Tennessee
-
LOUISIANA: Custom Workforce for Expanding
-
MARYLAND: Home of Innovators
-
MAINE: Yankee Ingenuity